What is a critical reference point within a specific system or process, and how does it impact overall efficacy?
A key reference point within a system or process. This point often serves as a benchmark for measurements, comparisons, or adjustments. It could be a specific data value, a calculated statistic, or a predefined condition. For instance, in quality control, a target standard deviation might represent the crucial reference point for ensuring product consistency. Alternatively, within a financial model, a particular interest rate could function as the core reference point for forecasting profitability.
This specific point's significance hinges on its ability to define a baseline or standard. This facilitates comparative analysis, enables performance evaluation, and guides corrective actions. Accurate identification and measurement of the reference point are crucial for efficient process optimization and effective decision-making. Historical context reveals a consistent human need to establish benchmarks; this fundamental practice is essential for any system demanding precision and reproducibility, ranging from manufacturing to scientific research.
The discussion of this critical reference point will now transition to explore its application in various industrial contexts, showcasing its practical importance in real-world scenarios.
SD Point
Understanding the significance of a reference point is crucial for effective analysis and decision-making. This point, often representing a standard or baseline, facilitates comparison and performance evaluation. Its precise definition is essential for optimizing processes and achieving desired outcomes.
- Reference
- Benchmarking
- Measurement
- Comparison
- Evaluation
- Adjustment
- Optimization
- Consistency
These aspectsreference, benchmarking, measurementinterrelate to create a system for evaluating performance and driving improvement. A well-defined reference point (SD Point) allows for the comparison of various data points against a standard, enabling organizations to identify areas needing adjustment. For instance, in manufacturing, a target standard deviation (SD Point) might be the reference for ensuring product consistency. By establishing and using the SD point, quality control procedures can efficiently evaluate and optimize manufacturing processes. The iterative process of measurement, comparison, and adjustment enables continuous improvement.
1. Reference
A reference point, fundamental to any system requiring precision and reproducibility, provides a crucial standard against which other data or metrics can be evaluated. In the context of an "SD point," the reference establishes a baseline for measurement and comparison, enabling the identification of deviations and adjustments necessary for optimization. A clear understanding of this reference is essential for evaluating performance and achieving desired outcomes within the system.
- Defining the Baseline
A reference point clearly defines the initial state or standard. This baseline is essential for comparative analysis. For instance, a target yield rate in a manufacturing process serves as the reference. Variations from this rate, positive or negative, can then be quantified and analyzed in relation to the reference. This allows for a focused investigation of factors contributing to either improvements or discrepancies.
- Facilitating Measurement Accuracy
The reference point provides a fixed standard for measurement instruments. Calibration against a reference standard ensures accuracy and consistency. This is vital for reliable data collection within any system. Without a defined reference point, the resulting data may lack objectivity and impede the process of evaluating the system's performance.
- Driving Process Optimization
By identifying deviations from the reference point, process improvements become quantifiable and actionable. Understanding the factors leading to deviations is key, potentially prompting adjustments to optimize efficiency. For instance, if a manufacturing process is consistently producing products with variations from the reference standard (SD point), analysis can pinpoint the root cause allowing for the implementation of solutions, thereby achieving greater consistency.
- Ensuring Consistency and Reproducibility
A reference serves as a foundation for ensuring consistent results. This is crucial in repeatable processes, where the ability to reproduce outputs is critical. In scientific experiments, a reference standard enables verifiable results and repeatable procedures. A consistent reference point underpins reliability and reduces experimental error, underpinning the pursuit of dependable conclusions.
In summary, a reference point, especially within the framework of an "SD point," acts as a cornerstone for precise measurement, comparative analysis, and process optimization. By establishing a clear baseline, measurement accuracy is improved, consistency is ensured, and effective decision-making about process adjustments is facilitated.
2. Benchmarking
Benchmarking, as a systematic process of measuring and comparing one's performance against a standard, is intrinsically linked to the concept of an "SD point" (standard deviation point). An "SD point," representing a critical reference point within a system, often serves as the benchmark against which performance is assessed. This relationship is fundamental because effective benchmarking necessitates a clear understanding of the reference against which performance is to be measured. Without a defined standard deviation point (SD Point), the process of benchmarking lacks a reliable framework, making comparisons inconclusive and potentially misleading. The selection and application of the benchmark, therefore, determine the accuracy and relevance of the assessment.
The importance of benchmarking as a component of an "SD point" lies in its ability to illuminate areas for improvement. For example, in manufacturing, a target standard deviation (SD point) might represent optimal product quality. Benchmarking against this SD point, by meticulously measuring deviation from this standard, helps pinpoint factors that negatively impact the uniformity of the product. Analyzing these deviations in relation to the SD Point provides invaluable insights for implementing corrective measures, enhancing efficiency, and ultimately improving the quality of the overall output. Likewise, in financial performance evaluations, a benchmark interest rate can represent a key reference point against which performance is judged, exposing deviations from the target rate and prompting strategical responses. Without this benchmark, performance assessments remain abstract and devoid of a quantifiable standard. Consequently, practical applications of benchmarking in different fields frequently involve careful identification and selection of the appropriate "SD point."
In conclusion, the effective implementation of benchmarking hinges on the robust establishment of an "SD point." By defining a clear standard of performance, benchmarking facilitates meaningful comparisons, allowing organizations and systems to identify areas requiring attention and implement targeted improvements. Challenges may arise from selecting a suitable and pertinent SD point. However, acknowledging the fundamental link between benchmarking and the SD Point ensures a structured approach to evaluation and drives a continuous cycle of process improvement.
3. Measurement
Accurate measurement is fundamental to the concept of a standard deviation point (SD point). The SD point, representing a critical reference within a system or process, inherently relies on precise measurement. Without reliable measurement, determining deviation from the SD point becomes impossible. Inherent in this relationship is the understanding that the accuracy of the measurement directly influences the validity of conclusions drawn from analysis of the SD point. Variability, a frequent characteristic in many systems, is often measured against the established SD point. Examples range from manufacturing processes (measuring product dimensions against a target value) to financial markets (assessing interest rates against a benchmark).
The critical role of measurement as a component of the SD point necessitates consideration of measurement tools and techniques. The choice of instruments, methodologies, and calibration procedures significantly impacts the accuracy of the data collected. For instance, in quality control, precise instruments measuring dimensions must be properly calibrated to ensure consistent and reliable data. This accuracy is paramount to accurately identifying deviations from the SD point, a key indicator of process stability and potential areas for improvement. Inconsistent or inaccurate measurement methods lead to misleading conclusions about the system's performance relative to the SD point.
In conclusion, measurement is inextricably linked to the significance of the SD point. Precise and reliable measurement forms the bedrock for evaluating performance against the established standard. Understanding the intricacies of measurement methods and their impact on the accuracy of the SD point is critical for sound decision-making and the optimization of processes. Challenges in this area include the complexity of certain systems or processes, requiring specialized measurement techniques, and the inherent limitations of instruments and measurement methodologies. Nevertheless, consistent and accurate measurement procedures are essential for evaluating and improving a wide range of systems.
4. Comparison
Comparison is integral to understanding and utilizing a standard deviation point (SD point). The SD point, representing a critical reference, necessitates comparison to assess deviation and identify areas requiring adjustment. A comparison against this benchmark reveals performance relative to the established standard. For example, in manufacturing, comparing product dimensions to the target values (the SD point) identifies deviations and guides corrective actions. Similarly, in financial markets, comparing current interest rates to a benchmark rate highlights variances and informs investment strategies.
The significance of comparison within the context of an SD point stems from its ability to illuminate discrepancies. By comparing data points to the SD point, anomalies become apparent, allowing for targeted analysis and problem-solving. Without comparison, the meaning of the SD point remains ambiguous, lacking the context necessary for effective decision-making. Comparative analysis facilitates a quantitative understanding of performance, providing concrete metrics for improvement. This comparative approach is crucial for identifying trends, patterns, and inefficiencies within a system, leading to optimized outcomes. In a quality control setting, comparing defect rates to the acceptable deviation (SD point) guides the implementation of corrective measures to maintain or improve quality.
In summary, comparison plays a vital role in leveraging the SD point. It provides the means to quantify deviations from the benchmark, enabling targeted interventions to optimize performance. By establishing a clear standard (SD point) and comparing actual data against it, systems can identify areas for improvement and maintain a consistent, optimal state. This comparative process ensures data-driven decision-making, driving continuous improvement. Challenges may arise if appropriate or relevant standards (SD points) are not correctly defined, diminishing the effectiveness of comparative analysis. Nevertheless, accurate comparison with a clearly established SD point yields quantifiable data, vital for efficient evaluation and process optimization within various contexts.
5. Evaluation
Evaluation, a critical component of any system employing a standard deviation point (SD point), assesses performance against the established benchmark. The SD point serves as the standard, while evaluation quantifies the degree of conformance or deviation. This relationship is essential because the evaluation process identifies areas needing adjustment, enabling optimization. For example, in a manufacturing setting, the SD point might represent the acceptable range for product dimensions. Evaluation, in this case, involves measuring each product against the SD point to determine whether it falls within the acceptable parameters. If not, the evaluation reveals the extent of the deviation, guiding remedial action for improved product consistency.
The importance of evaluation within the SD point framework lies in its capacity to identify trends and patterns. By continuously evaluating performance against the SD point, organizations can anticipate potential issues, enabling proactive measures to maintain desired outcomes. Consider a financial model using an SD point representing a target return on investment. Regular evaluation of actual returns against the SD point enables timely adjustments to strategies and safeguards against unexpected variances. Similarly, in scientific experiments, evaluation of data against the SD point is crucial for recognizing outliers and refining methodologies, leading to greater accuracy and consistency in results.
In conclusion, evaluation, when integrated with an SD point, provides a structured approach to performance assessment. The process of comparing actual results to the established SD point allows for the identification of variances, the analysis of trends, and the implementation of corrective actions. This data-driven approach promotes consistency, enhances efficiency, and contributes to the achievement of desired outcomes across diverse fields. While the specific techniques of evaluation might vary, the fundamental connection between evaluation and the SD point remains crucial to optimizing performance and achieving consistent results.
6. Adjustment
Adjustment, in the context of a standard deviation point (SD point), represents a crucial step in refining processes and achieving desired outcomes. Deviations from the SD point necessitate adjustments to realign performance with established benchmarks. This process involves identifying the cause of the deviation, implementing corrective measures, and monitoring the impact of these changes. The effectiveness of these adjustments is directly related to the accuracy of the underlying data and the depth of analysis applied to the problem.
- Identifying the Root Cause
Accurately determining the source of deviation from the SD point is paramount. This often involves a detailed analysis of contributing factors, encompassing both internal and external elements influencing the system. For example, in manufacturing, if product dimensions consistently deviate from the SD point representing acceptable tolerances, investigation might reveal issues with machinery calibration, material inconsistencies, or procedural errors. Identifying the root cause is foundational to developing targeted and effective adjustments.
- Implementing Corrective Measures
Once the root cause of deviation is identified, appropriate corrective measures can be implemented. These measures might involve recalibrating equipment, adjusting production parameters, retraining personnel, or procuring higher-quality materials. The choice of corrective action depends heavily on the specific circumstances and the nature of the deviation from the SD point. The objective is to bring the process back within the acceptable tolerances defined by the SD point. This requires careful planning, consideration of potential impacts, and a systematic approach to implementation.
- Monitoring and Evaluating Adjustments
Monitoring the effects of implemented adjustments is essential. This entails tracking key performance indicators (KPIs) and evaluating whether the adjustments successfully bring performance back in line with the SD point. Continuous monitoring facilitates timely intervention if the adjustments prove ineffective or lead to unintended consequences. For instance, in financial modeling, a model's performance deviating from the SD point (projected returns) might necessitate adjustments to inputs or variables, which are then monitored to confirm a return to the desired parameters. This ongoing evaluation is critical to ensure long-term effectiveness.
- Iterative Refinement
Adjustment is not a one-time action but an iterative process. The identification of persistent deviations or unintended consequences necessitates further adjustments, reflecting an ongoing commitment to optimizing performance against the SD point. This iterative refinement ensures continuous improvement and adaptability to changing circumstances. In research, an experiment might need repeated adjustments to the experimental design based on the results, until the SD point is reached and a valid outcome is achieved.
In conclusion, adjustment, when applied strategically in conjunction with a clearly defined SD point, is instrumental in optimizing processes. By pinpointing the root causes of deviations, implementing targeted measures, and meticulously monitoring results, organizations can consistently achieve and maintain desired performance metrics. The cyclical nature of this process identification, implementation, monitoring, and refinement demonstrates the dynamic nature of utilizing an SD point and underscores its role in driving continuous improvement.
7. Optimization
Optimization, in the context of a standard deviation point (SD point), represents a crucial process aimed at maximizing the efficiency and effectiveness of a system or process relative to the benchmark defined by the SD point. Achieving optimal performance hinges on minimizing deviations from this pre-defined standard. The importance of optimization as a component of the SD point lies in its ability to minimize variances and maintain a consistent, optimal state. Consider manufacturing processes; an SD point representing acceptable product dimensions mandates optimized production methods to consistently generate products within those tolerances. This optimized approach not only enhances product quality but also minimizes waste and increases overall production efficiency.
Practical applications of this understanding are pervasive. In financial modeling, an SD point might represent projected returns. Optimization strategies, such as portfolio diversification or targeted investment decisions, become critical to aligning actual returns with the projected standard (SD point). Similarly, in scientific research, an SD point might denote acceptable margin of error. Optimized experimental designs and data analysis procedures are crucial for minimizing deviations and maximizing the reliability of results. Furthermore, efficient resource allocation within organizations be it time, capital, or personnel can be seen as optimization strategies aiming to achieve desired outcomes within pre-determined parameters established by relevant SD points.
In conclusion, optimization and the SD point are inextricably linked. Optimization strategies are essential for minimizing deviations from the SD point and maintaining consistent, optimal performance within a system. This understanding facilitates the development of effective approaches for achieving desired outcomes across various fields. Challenges often arise from identifying the precise SD point or implementing optimal strategies within complex systems. However, the recognition of optimization as a direct facilitator of conformance to the SD point is key for achieving consistent, high-quality performance and driving continuous improvement.
8. Consistency
Consistency, a critical attribute in any system, is fundamentally linked to a standard deviation point (SD point). Maintaining a consistent state within a defined range relative to the SD point is essential for reliable performance and predictable outcomes. This connection rests on the ability of a system to consistently produce results within the parameters set by the SD point. Deviation from the expected standard inherent in an SD point necessitates analysis and adjustment for the restoration of consistency.
- Predictability and Reliability
A consistent system produces predictable outputs. This predictability is a direct outcome of maintaining results within the boundaries set by the SD point. For instance, in manufacturing, consistent product dimensions relative to a target standard (SD point) ensure reliability in end-use applications. Without consistency, systems become unreliable, increasing risk and reducing confidence in the outputs.
- Reduced Variability and Error
Consistency minimizes variability in outcomes. Reducing error and variability is a direct result of maintaining processes within the defined parameters of the SD point. In scientific experiments, consistency in experimental procedures leads to repeatable results, reducing experimental errors and increasing confidence in conclusions. High variability frequently indicates a need for adjustment to bring the system back into alignment with the SD point.
- Enhanced Efficiency and Productivity
Consistent performance within the boundaries of the SD point typically improves operational efficiency. In industrial settings, consistent production rates relative to a target yield (SD point) maximize output and reduce waste. Inconsistency, on the other hand, introduces inefficiencies, as resources are consumed unnecessarily or efforts are wasted in trying to compensate for variance.
- Improved Quality and Reduced Waste
Consistency usually translates to improved quality relative to the SD point. In quality control, consistent adherence to predefined standards (SD point) minimizes defects, reduces waste, and ultimately enhances the overall quality of the final product. Fluctuations in quality, on the contrary, indicate a need for process optimization and adjustment to bring the process back to compliance with the SD point.
In conclusion, consistency and the SD point are interwoven. A system that consistently produces results within the parameters defined by the SD point exhibits enhanced predictability, reliability, efficiency, and quality. Maintenance of consistency requires ongoing monitoring, analysis, and appropriate adjustments where deviations from the SD point are observed, ensuring the system functions optimally within its defined parameters.
Frequently Asked Questions about Standard Deviation Point (SD Point)
This section addresses common inquiries regarding the concept of a Standard Deviation Point (SD Point) and its practical application. Questions cover its definition, significance, and the challenges associated with its implementation.
Question 1: What exactly is a Standard Deviation Point (SD Point)?
A Standard Deviation Point (SD Point) represents a specific value or threshold used as a benchmark for measuring variability or deviation within a given system or process. It defines a specific point on the standard deviation curve, frequently used to indicate acceptable ranges of variation or the margin of error within a data set. This point is crucial for understanding and controlling process variations and for ensuring consistency.
Question 2: How is an SD Point determined?
Determining an SD Point involves statistical analysis of data collected from the system or process. Calculations focus on identifying the average and standard deviation within the dataset. The SD Point is a value calculated from this analysis, representing a predetermined level of acceptable variation. Careful consideration of context is essential; the SD Point should be relevant to the specific system or process in question.
Question 3: Why is an SD Point important in different contexts?
An SD Point is vital in various fields for maintaining quality and consistency. In manufacturing, it ensures product tolerances remain within acceptable limits, minimizing defects. In financial analysis, it helps establish acceptable risk levels and performance parameters. In scientific research, it facilitates the validation and reproducibility of results. An SD Point serves as a crucial reference for evaluating performance, driving improvements, and making informed decisions.
Question 4: What challenges can arise when working with SD Points?
Implementing an SD Point can present challenges. Data collection methods, calculation accuracy, and the choice of an appropriate SD Point (e.g., specific percentile) can influence results. In addition, changes within the system over time or unforeseen external factors can affect data and require periodic recalibration of the SD point. Interpretation of results and the implementation of adjustments can also be challenging.
Question 5: How does an SD Point contribute to process optimization?
An SD Point is fundamental for process optimization. By establishing a clear benchmark, deviations from the SD Point become readily identifiable, facilitating the identification of areas needing improvement. This analysis allows for focused corrective actions and ongoing monitoring, leading to consistent performance and minimized errors within the system, optimizing efficiency and quality.
Understanding the SD Point is crucial for any system or process requiring precision, consistency, and dependable results. Careful consideration of its implications is fundamental in various applications.
This concludes the FAQ section, and the next section will delve into the practical application of SD Points in a specific industry example.
Conclusion
This exploration of the standard deviation point (SD point) highlights its critical role in diverse systems. The SD point, acting as a benchmark, facilitates precise measurement, comparison, and evaluation of performance. Establishing an SD point enables the identification of deviations, driving targeted adjustments for optimization. Key aspects discussed include defining the baseline, ensuring measurement accuracy, optimizing processes, and maintaining consistency. The iterative nature of adjustment, encompassing root cause analysis, corrective measures, and continuous monitoring, is crucial for sustainable improvement. The analysis underscores the significance of benchmarking in various contexts, ranging from manufacturing to financial modeling and scientific research, to achieve optimal outcomes within defined parameters.
The significance of a well-defined SD point extends beyond simple measurement. It provides a structured approach to identify potential issues, anticipate problems, and implement corrective actions. A comprehensive understanding of the SD point's application empowers organizations and individuals to optimize processes, enhance efficiency, and improve quality. Future research should explore the application of advanced statistical methodologies and technological advancements to refine the determination and utilization of SD points in more complex systems.

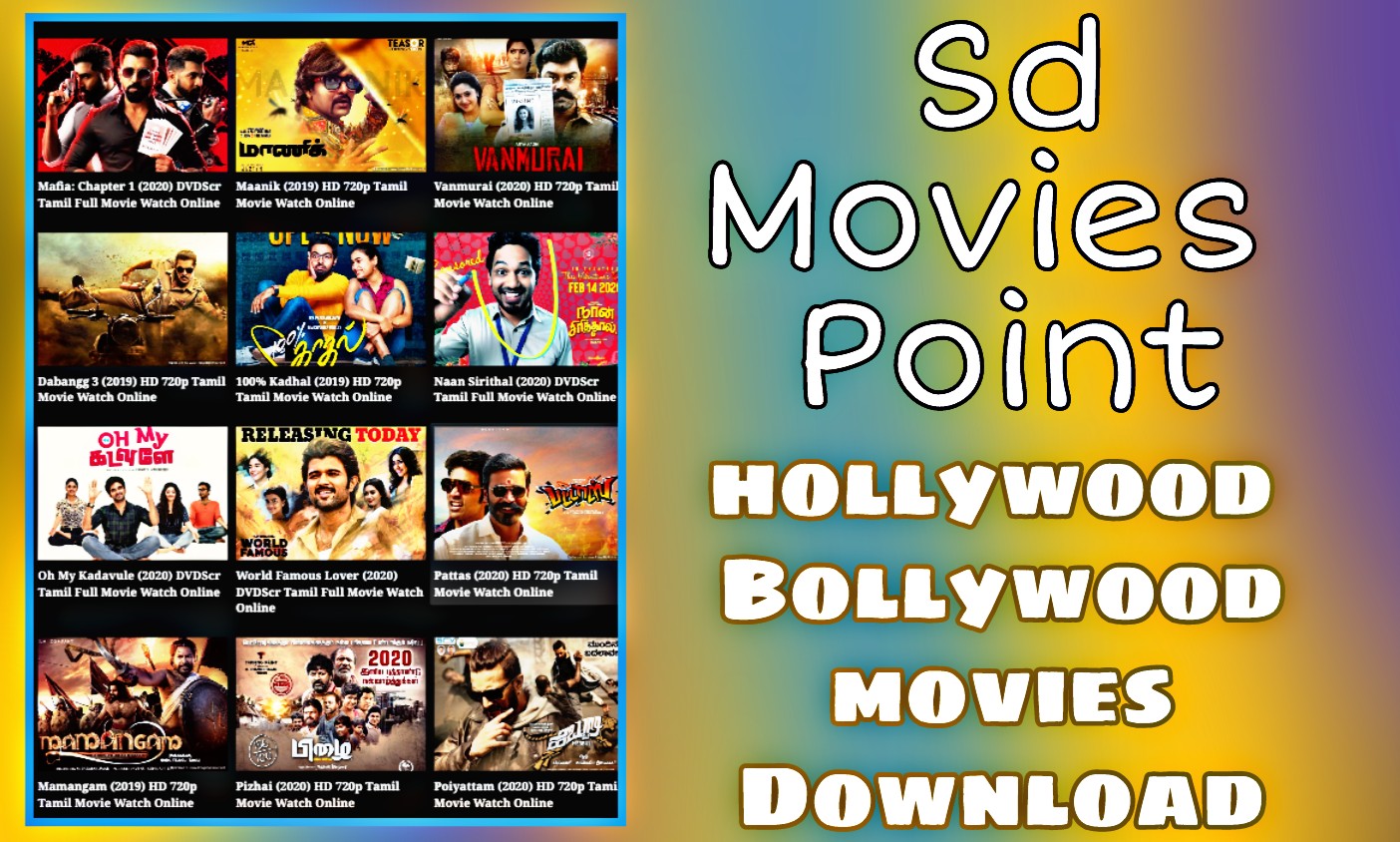
